How to Build a Drone Army to Conquer the $208 Billion Sky: A US Manufacturing Blueprint
The US drone manufacturing capacity faces a critical inflection point. The global drone market presents a massive opportunity for domestic production, valued at $33.2 billion in 2024 and projected to reach $208.38 billion by 2032. However, Chinese dominance — exemplified by DJI's 70% US market share — creates significant challenges for establishing competitive domestic drone supply chain operations. This analysis provides a strategic roadmap for US companies seeking to build drone manufacturing capabilities at scale, examining component-level drone component sourcing dynamics, production scenarios, and engineering innovations that could transform the competitive landscape. For manufacturing executives and supply chain leaders, this blueprint offers actionable insights to navigate regulatory tailwinds, leverage domestic strengths, and identify collaborative opportunities across the emerging US drone ecosystem.
The Strategic Imperative: Why US Drone Manufacturing Matters Now
The global drone landscape is at an inflection point. With 33% of US commercial drone use happening in agriculture, 22% in logistics, 20% in defense, and 15% in public safety, the market's strategic importance extends far beyond consumer applications. Yet Chinese manufacturers continue to dominate through scale advantages, established supply chains, and systematic cost leadership.
Three concurrent forces are creating unprecedented momentum for domestic drone manufacturing:
- Policy Shifts: Recent tariffs (34% on Chinese goods as of April 2025) and security-focused regulations such as the Countering CCP Drones Act have created a protective environment for domestic producers. These measures reflect growing concerns about data security and supply chain resilience rather than mere protectionism.
- Supply Chain Repatriation: Major investments such as TSMC's $40 billion Arizona semiconductor plant signal a broader industrial repatriation trend, establishing critical infrastructure for complex electronics manufacturing.
- Market Expansion: The drone market's 25% compound annual growth rate creates space for new entrants alongside established players, particularly in specialized applications where customization and compliance matter more than raw cost.
For manufacturing strategists, these convergent trends present a rare opportunity to enter a high-growth market with meaningful competitive advantages beyond price. The question isn't whether domestic drone production makes sense, but rather how to execute effectively at different scales of ambition.
Deconstructing the Drone: A Component-Level Analysis
Understanding drone manufacturing begins with a comprehensive breakdown of the bill of materials (BOM). Below, we analyze each major component through the dual lenses of technical requirements and supply chain dynamics, with particular attention to domestic sourcing potential.

Frame/Chassis: The Structural Foundation
Current State: Carbon fiber dominates high-performance frames (70% of premium drones), with China's Toray subsidiaries controlling 60% of global supply (20,000 tons annually) and Japan's Toray holding another 30% market share. US producer Hexcel currently trails at 15% market share.
Supply Chain Insights:
- Bottlenecks: Resin supply (70% from Chinese BASF operations) and specialized molding expertise (concentrated in Shenzhen's ~500+ factories) represent significant constraints.
- US Opportunity: Hexcel (Utah) produces 1,500 tons annually but could expand to 4,500 tons with $100 million in strategic investment. Alternative materials from Solvay (Georgia), including PEEK thermoplastics, could reduce Chinese resin dependency by approximately 20%.
- Strategic Consideration: Nearshoring to Mexico (particularly CNC shops in Tijuana) could reduce shipping costs by 15% (~$3 per unit) while maintaining North American supply chain integrity.
Motors: The Power Center
Current State: Brushless DC motors using neodymium magnets form the industry standard, with Chinese manufacturer T-Motor holding 50% global market share (~2 million units annually). China's 90% control of global neodymium supply (~200,000 tons annually) creates significant leverage.
Supply Chain Insights:
- Bottlenecks: Rare earth refining (95% Chinese, with Malaysian Lynas at 4%) and winding automation (China's 80% robotic line share versus 20% in the US) limit domestic capacity.
- US Opportunity: MP Materials (California) is mining ~45,000 tons of rare earths annually — sufficient for ~5 million motors — while Oransi Inc. (Virginia) produces thousands of motors annually, with the capacity to scale with investment.
- Strategic Consideration: India's recent $50 million motor manufacturing investment could yield ~50,000 units annually by 2027, offering supply diversity outside the China-US dynamic.
Batteries: The Flight Duration Determinant
Current State: Lithium-ion batteries remain the dominant power source, with Chinese manufacturers CATL (37% market share, 200 GWh annually) and BYD (10% market share, 50 GWh annually) — with 70% global battery production in China — far outpacing US producers Tesla and Amprius (combined 15% market share).
Supply Chain Insights:
- Bottlenecks: Lithium refining (80% Chinese control, 15% Australian) and cell assembly (China's 1,000+ plants versus ~10 in the US) severely constrain domestic output.
- US Opportunity: Amprius (Colorado) is pioneering silicon-anode technology (500 Wh/kg) while Tesla's Nevada facilities produce 37 GWh+ annually. Strategic lithium sourcing from Chile could diversity supply.
- Strategic Consideration: Solid-state battery pilots at QuantumScape (projected 1 GWh by 2027) could shift 10% of the market away from Chinese dominance, according to 2024 IEEE assessments.
Flight Controllers: The Intelligence Hub
Current State: The drone's central processor typically uses STM32F7 microcontrollers and specialized sensors, with Chinese manufacturer Holybro producing hundreds of thousands of units annually and Taiwan's TSMC fabricating 80% of necessary microcontrollers. US company Qualcomm holds just 5% market share.
Supply Chain Insights:
- Bottlenecks: Semiconductor supply (dominated by TSMC with 90% of drone-specific MCUs) and firmware expertise (China's estimated 1,000+ engineers versus roughly hundreds in the US).
- US Opportunity: Qualcomm's NDAA-compliant chips and NVIDIA's AI-focused Jetson platform leverage US technology leadership, while TSMC's Arizona operations could add additional production capacity by 2027.
- Strategic Consideration: The open-source PX4 flight control software (primarily US-developed) reduces development costs by approximately 30% ($10 per unit) but faces competition from proprietary Chinese firmware with faster market deployment.
Scale Economics: Pathways to Competitive Production
Drone manufacturing economics vary dramatically based on production volume, with corresponding implications for market strategy and investment requirements. Three distinct scenarios emerge:
Small-Batch Production (1,000-10,000 units annually)
Approach: Leveraging 3D printing (Markforged, ~$50,000 initial investment) with manual assembly (approximately 20 hours per unit).
Economics: ~$2,000 per unit cost structure, challenging when competing against $500 mass-produced alternatives.
Market Opportunity: Public safety applications offer immediate potential, with approximately 10,000 Chinese drones potentially replaceable due to security concerns.
Strategic Considerations:
- Focus on customization, specialized payloads, and security certifications that justify premium pricing
- Emphasize short lead times and adaptability as key value propositions
- Consider contract manufacturing partnerships to reduce capital expenditure
Medium-Scale Production (10,000-100,000 units annually)
Approach: Repurposing existing manufacturing facilities (example: GM, estimated $20 million retrofit, 12-month timeline) to achieve 100 units daily through partial automation.
Economics: ~$1,000 per unit cost structure, competitive in specialized market segments.
Market Opportunity: Defense applications, particularly aligned with Department of Defense "Replicator" initiative targeting "thousands" of autonomous systems.
Strategic Considerations:
- Invest in automation for labor-intensive processes (soldering, testing) while maintaining flexibility
- Develop domestic supplier partnerships backed by multi-year commitments
- Create modular designs that can serve multiple market segments with minimal retooling
Mass Production (100,000-1,000,000 units annually)
Approach: Purpose-built highly automated facilities (example: Red Cat's Utah facility, $60 million investment) achieving 100 units hourly.
Economics: ~$600 per unit cost structure, narrowing the gap with Chinese alternatives.
Market Opportunity: Broader commercial market, addressing a significant portion of the 853,857 FAA-registered drones.
Strategic Considerations:
- Vertical integration of critical components to reduce supply chain vulnerability
- Strategic partnerships with key technology providers (TSMC, NVIDIA, Amprius)
- Lobbying for expanding government incentives to match China's estimated $12 billion sector investment
Hybrid US-Mexico Approach
Approach: Silicon Valley R&D combined with Tijuana-based assembly operations ($10 million initial investment).
Economics: ~$800 per unit cost structure, balancing innovation capabilities with competitive manufacturing costs.
Market Opportunity: Blended strategy allowing parallel penetration of premium and mid-market segments.
Strategic Considerations:
- Allocate high-intellectual-property operations (firmware, design) to US facilities
- Leverage Mexico's established electronics manufacturing ecosystem
- Develop robust cross-border logistics capability (~$40 per unit, but manageable within cost structure)
Case Study: Skydio's Approach to Domestic Manufacturing
Skydio provides a compelling example of successful US-based drone manufacturing in a Chinese-dominated market. Founded in 2014, the California-based company has achieved several key milestones that illustrate viable pathways for domestic production:
Strategic Differentiation: Rather than competing directly on price, Skydio focused on advanced autonomy capabilities that Chinese competitors couldn't easily replicate. Their obstacle-avoidance technology created a defensible market position in specialized applications such as infrastructure inspection and public safety.
Domestic Production Scale: Skydio's manufacturing facility in Hayward, California, produces thousands of units annually — modest compared to DJI's millions but sufficient to serve targeted segments profitably. This "right-sized" approach avoided the capital-intensive trap of attempting to match Chinese production volumes immediately.
Regulatory Leverage: By securing "Blue sUAS" certification and ensuring NDAA compliance, Skydio successfully captured government and defense contracts where Chinese alternatives were explicitly prohibited. This created a protected market segment with less price sensitivity.
Vertical Integration: Unlike many consumer electronics companies, Skydio maintains control over both hardware and software development, reducing dependency on Chinese firmware and creating performance advantages that justify premium pricing.
Results: Skydio achieved unicorn status with a $1 billion+ valuation in 2021 while maintaining domestic production, demonstrating that US manufacturing can be financially viable with the right strategic approach. Their success template emphasizes specialization before scale and regulatory advantage before price competition.
Key Takeaway: Domestic manufacturers should emulate Skydio's focus on defensible technology advantages and strategic market selection rather than attempting to replicate Chinese cost structures immediately.
Engineering for Competitive Advantage
Beyond scaling conventional production, several emerging engineering approaches could fundamentally alter the competitive dynamics of drone manufacturing:

Circular Manufacturing Models
The linear production model dominant in consumer electronics creates significant inefficiencies in material utilization. Boeing has demonstrated 70% carbon fiber reclamation is technically feasible, while Redwood Materials achieves 95% battery component recovery. Applied systematically to drone manufacturing, circular approaches could reduce costs by approximately 25% while significantly improving sustainability metrics.
Implementation Strategy: Start with high-value components (batteries, motors), design for disassembly from the outset, and establish reverse logistics partnerships with major commercial users.
AI-Optimized Supply Chain Management
Conventional supplier relationships and inventory management approaches struggle with the complexity of electronics supply chains. Advanced AI systems from providers such as Flexe and IBM Watson demonstrate 30% lead time reduction (from 30 to 10 days) and 20% lower audit costs ($5,000 per unit) through predictive analytics and dynamic sourcing.
Implementation Strategy: Begin with component-level tracking of critical items (semiconductors, batteries), expand to full bill of materials visibility, and ultimately develop predictive disruption models. Consider intelligent supply chain management tools such as Partsimony.
Energy Density Breakthroughs
Battery limitations remain the primary constraint on drone performance and utility. Solid-state battery technologies from companies such as QuantumScape promise 500 Wh/kg energy density — enabling 69-minute flight times compared to current 46-minute standards. While cost premiums exist now, economies of scale could eliminate this differential by 2027.
Implementation Strategy: Dual-track development using current lithium-ion technology while investing in solid-state partnerships; develop modular battery bays to enable rapid technology migration as new cells become available.
Swarm Intelligence Architectures
Individual drone capabilities face inherent physical limitations, but coordinated drone networks can achieve exponentially greater functionality. NVIDIA's Jetson Orin platform enables 50% lower latency in swarm communications, supporting fleets of 100+ drones operating as coordinated systems rather than individual units.
Implementation Strategy: Develop common communication protocols, invest in edge computing capabilities, and create simulation environments for testing complex multi-drone scenarios before physical deployment.
Biomimetic Design Approaches
Nature has already solved many aerodynamic and efficiency challenges through evolutionary processes. Owl-inspired propeller designs demonstrate 10 dB noise reduction (approximately half the perceived volume) with only $12 per unit cost impact, potentially opening significant new market applications in noise-sensitive environments.
Implementation Strategy: Partner with university research programs (example: Purdue University's $1 million biomimetics grant), focus on high-impact components (propellers, airframe), and quantify performance improvements across multiple parameters beyond cost.
Building a Resilient US Drone Ecosystem
Moving from isolated manufacturing initiatives to a robust domestic ecosystem requires strategic coordination across multiple stakeholders:
Semiconductor Sovereignty
Taiwan currently produces 92% of advanced drone semiconductors below 10nm. TSMC's Arizona expansion represents a critical step toward resilient supply, but needs complementary investments in design, packaging, and testing capabilities. Strategic partnerships between drone manufacturers and chip developers should include multi-year purchase commitments in exchange for capacity guarantees.
Workforce Development
The typical drone incorporates expertise across materials science, electrical engineering, software development, and advanced manufacturing. University partnerships (e.g., Purdue's drone technology center) should be complemented by specialized training programs focused on high-demand skills such as carbon fiber manufacturing and battery cell production.
Regulatory Harmonization
Fragmented drone regulations across federal agencies create unnecessary complexity for manufacturers. Industry coalitions should advocate for standardized security certification processes, particularly for commercial applications where Chinese alternatives may be restricted but clear compliance pathways remain undefined.
Supply Chain Transparency
Complex electronics remain vulnerable to counterfeit components and security compromises. Blockchain-based tracking systems (example: IBM Hyperledger) can ensure NDAA compliance while reducing audit costs by approximately 20% (~$5,000 per unit), creating both security and economic benefits.
Navigating Drone Manufacturing Regulations: Compliance Guide

The above covers a helpful framework in navigating drone manufacturing regulations. Compliance costs typically add 12-18% to manufacturing overhead but create defensible market segments with less price competition.
Implementation Roadmap: Building US Drone Manufacturing Capacity
For organizations pursuing domestic drone production, this phased implementation timeline provides strategic milestones:
Phase 1: Foundation Building (0-6 Months)
- Complete comprehensive supply chain mapping with vulnerability assessments
- Establish strategic partnerships with key domestic component suppliers
- Develop regulatory compliance strategy and certification roadmap
- Prototype initial designs optimized for US-based manufacturing
- Secure initial funding and establish minimum viable production capacity
Phase 2: Production Scaling (6-12 Months)
- Launch small-batch production (1,000-5,000 units)
- Implement component-level tracking system for regulatory compliance
- Establish quality assurance protocols specific to target market requirements
- Begin vertical integration of 2-3 critical components with highest vulnerability
- Develop workforce training programs with regional educational institutions
Phase 3: Market Expansion (12-24 Months)
- Scale to medium production volumes (10,000-50,000 units annually)
- Implement targeted automation for highest-labor components
- Expand domestic supplier network with multi-year commitments
- Develop specialized variants for high-value market segments
- Establish cross-border logistics for hybrid manufacturing models
Phase 4: Ecosystem Leadership (2-3 Years)
- Reach production targets of 100,000+ units annually
- Achieve 50%+ domestic content in bill of materials
- Establish innovation partnerships for next-generation technologies
- Lead industry standardization efforts for interoperability
- Develop circular manufacturing capabilities for key components
Conclusion: The Path Forward
China's established manufacturing ecosystem — producing 10.5 million drones annually at approximately $500 per unit — represents a formidable competitive challenge. However, the combination of policy tailwinds, technology innovations, and strategic investments creates a viable pathway to meaningful US market share.
Currently, ~70% of drone components being imported highlight immediate challenges, but companies such as Hexcel, Amprius, and Qualcomm provide foundation points for an expanding domestic supply base. A realistic scaling trajectory would target 1 million units annually by 2030, capturing 20-30% of the projected $208 billion market.
For manufacturing executives evaluating market entry, three principles should guide strategic planning:
- Start with Defensible Niches: Focus initial production on segments where regulatory advantages or specialized requirements create natural protection from price-based competition.
- Invest in Ecosystem Development: Allocate resources to supplier capability building, workforce development, and shared infrastructure rather than attempting vertical integration prematurely.
- Design for Future Economics: Engineer products with awareness of emerging technologies that could fundamentally alter cost structures within 3-5 years, particularly in battery technology, materials science, and automation.
Self-Assessment: Is Your Organization Positioned for Drone Manufacturing?

Score your organization from 1-5 in each area. A total score of 20+ suggests strong positioning for market entry.
The drone market represents more than just another consumer electronics category — it constitutes a foundational technology for the next wave of automation across multiple industries. Building manufacturing capabilities now positions companies not just for direct market participation, but for leadership in the broader autonomous systems revolution unfolding across the American economy.
About Partsimony
Partsimony helps hardware teams scale faster with fewer resources by building adaptive manufacturing supply chains that provide a decisive competitive edge.
To get more done faster and with fewer resources, reach out to solutions@partsimony.com.
-------
This analysis draws from industry data as of April 2025, including reports from FAA, Statista, DroneII, Hexcel, MP Materials, TSMC, IEEE, and other sources. Market projections should be validated against company-specific scenarios and investment parameters.
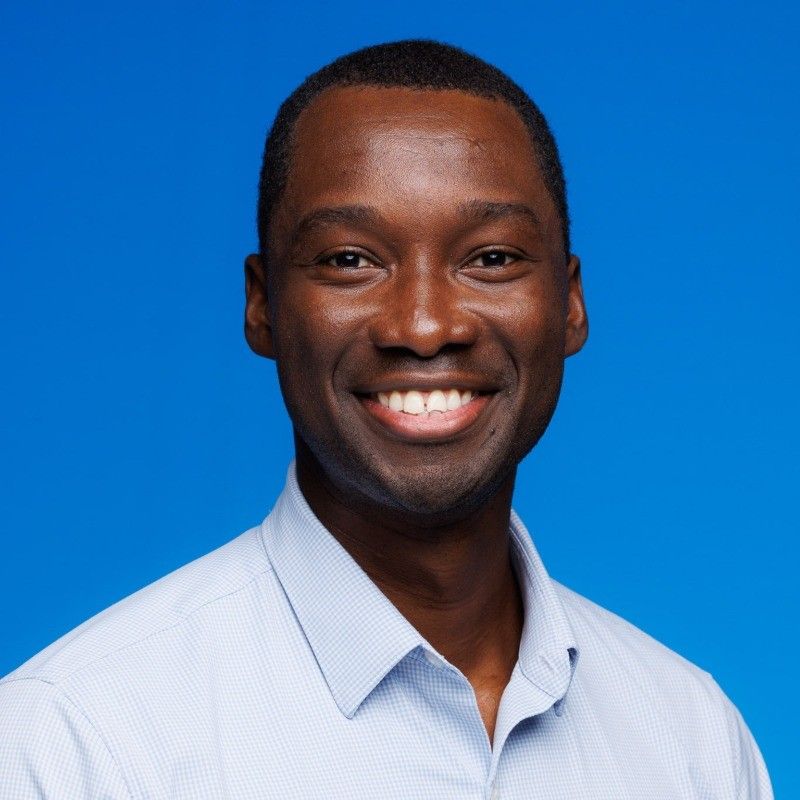
Rich Mokuolu
Supply Chain Strategist
Stay Updated
Get the latest insights on supply chain innovation and hardware development.