Overcoming Labor Shortages with Automation and Robotics: The Lifeline for Manufacturing & Supply Chains
How cutting-edge technologies are bridging workforce gaps, boosting efficiency, and reshaping the future of industry in 2025
The manufacturing and supply chain sectors currently face an unprecedented confluence of workforce challenges. With a projected 2.1 million worker shortfall by 2030 and more than 20% of plants currently citing labor as a constraint, organizations are confronting a fundamental shift in how production needs to operate.
Automation and robotics have evolved from strategic advantages into operational necessities. This analysis explores how these technologies effectively solve workforce challenges, drive measurable productivity gains, and create sustainable operations that don't depend on an ever-expanding human workforce. We examine implementation strategies, ROI frameworks, and practical approaches for organizations at any stage of their automation journey.
The Expanding Labor Gap: A Structural Challenge
The initial perception that labor shortages were merely a temporary pandemic disruption has been thoroughly disproven. The data tells a compelling and concerning story.
A 2024 Deloitte and Manufacturing Institute study now projects a staggering 2.1 million worker shortage in U.S. manufacturing by 2030 – up from earlier estimates of 1.9 million. This isn't just about COVID disruption; it's about accelerating retirements and insufficient new talent entering the industrial workforce.
Warehousing isn't faring any better. Despite employment peaking at 1.44 million workers in July 2021, the sector faces annual turnover rates of 46% – nearly half the workforce changing every year, largely driven by relentless e-commerce growth demanding more personnel.
"We're seeing a structural shift, not a cyclical one," is becoming a common refrain among operations leaders. The Quarterly Survey of Plant Capacity Utilization (QSPC) backs this up: 20.6% of U.S. manufacturing plants cited labor shortages as a direct constraint on production in Q3 2024. While that's better than the 46.3% peak during COVID's worst days, it's still nearly double the 2014-2016 average of 10.7%.
These shortages create direct financial pressure. Warehouse wages jumped from $14.83 per hour in Q1 2019 to $22.47 by June 2021 – a 51% increase in just over two years. This wage inflation has significantly outpaced most companies' ability to increase selling prices, creating substantial margin pressure.
From Strategic Option to Operational Necessity
As a result of labor becoming scarcer and more expensive, automation and robotics have transitioned from "nice-to-have" innovations to essential components of a sustainable operation.
The adoption data confirms this shift. According to MHI's annual survey, 38% of supply chain leaders were already using robotics in 2021, with another 38% planning adoption by 2026. Even more telling? By 2022, 53% of respondents reported increasing their investment in these technologies.
This adoption extends beyond traditional robotics strongholds. North American robot orders increased 20% in Q1 2021 compared to the previous year, with non-automotive sectors (including food processing and consumer goods) growing even faster at 32%.
Globally, the International Federation of Robotics (IFR) reports 2 million industrial robots now in operation worldwide in 2025, growing at a compound annual rate of 14% since 2019 – dramatically outpacing human workforce expansion in manufacturing.
"The business case for automation has fundamentally changed," a supply chain director at a mid-sized food manufacturer recently noted. "With wages up over 50% and positions still going unfilled, projects that didn't make financial sense three years ago are now no-brainers."
Strategic Applications Delivering Immediate Value
The most successful implementations target specific operational pain points with appropriate technology solutions:
Workforce Multiplication: Locus Robotics' autonomous mobile robots (AMRs) effectively make existing warehouse workers 2-3 times more productive while reducing overall labor requirements by 20-30%. These systems amplify the capabilities of your existing team.
Repetitive Task Automation: Collaborative robots (cobots) from companies such as Universal Robots have demonstrated particular value in assembly operations where precision and consistency are key. Implementations at manufacturers such as Nissan have reduced assembly time by 10% while freeing human workers for higher-value activities.
Demand Spike Management: For operations with significant seasonal variability, robotics provides critical flexibility. XPO Logistics deployed 5,000 robots by 2023, enabling them to manage holiday surge periods with 30% fewer seasonal hires – a significant advantage when temporary workers are increasingly hard to find and expensive to onboard.

Real Companies, Real Results: Implementation Case Studies
The transition from theoretical potential to operational reality is happening right now across multiple sectors. The following case studies demonstrate how organizations are implementing automation to directly offset labor constraints.
DHL: Focused Implementation in Fulfillment Operations
Challenge: DHL faced a 15% staffing shortfall during the 2021 peak season, threatening their ability to meet customer commitments.
Solution: A strategic deployment of Locus Robotics AMRs across multiple fulfillment centers, creating a hybrid human-robot workforce model. The robots handled the monotonous travel between pick locations, while humans focused on the dexterity-requiring task of actual item selection.
Results: Throughput increased by 200% in some facilities while dependence on hard-to-find temporary labor dropped by 25%. The implementation supported ongoing operations despite persistent staffing challenges.
Integration Approach: DHL began with a pilot at a single facility, refining workflows and integration with their WMS before broader deployment. This phased implementation allowed for employee training and workflow optimization before scaling.
Amazon: Systematic Enterprise-Wide Transformation
Challenge: Despite employing 520,000 workers in 2021, Amazon faced persistent turnover challenges and increasing labor costs in its fulfillment network.
Solution: By 2025, they expanded their robotics fleet to include 200,000 units, with specialized Kiva systems now handling approximately 40% of picking tasks – the most labor-intensive part of warehouse operations.
Results: A 15% reduction in fulfillment costs while maintaining capacity despite workforce limitations. The robotic systems also created a more sustainable work environment by eliminating many physically demanding tasks that contributed to fatigue and injury.
Workforce Transition Strategy: Amazon implemented a comprehensive retraining program, shifting many floor workers to robot supervision and maintenance roles, with tuition support for those seeking technical certifications.
BMW: Precision Implementation for Skilled Labor Gaps
Challenge: BMW's German manufacturing operations faced a 10% gap specifically in skilled labor by 2023, threatening production of precision components.
Solution: Implementation of 400 collaborative robots (cobots) focused on assembly and inspection processes requiring consistent precision. These machines worked alongside experienced technicians, handling repetitive precision tasks.
Results: An 8% increase in output with the existing workforce while maintaining quality standards – demonstrating how automation can address both quantity and quality dimensions of the labor shortage.
Industry-Specific Considerations: For high-precision manufacturing such as automotive, BMW found that cobots' ability to maintain consistent tolerances actually improved quality metrics by 12% while reducing rework.
Starting Your Automation Journey: A Phased Approach
Organizations at different stages of automation maturity require different implementation approaches. Here's a practical framework for getting started or advancing your current efforts:
Phase 1: Assessment and Targeting (1-2 Months)
- Conduct detailed workflow analysis to identify specific labor-intensive processes
- Prioritize automation targets based on labor requirements, process stability, and complexity
- Develop initial ROI projections for targeted processes
- Begin stakeholder engagement and communication planning
Phase 2: Solution Development (1-2 Months)
- Research applicable technology solutions for prioritized processes
- Conduct vendor evaluations using standardized criteria
- Develop detailed implementation requirements and integration points
- Create comprehensive financial models and ROI projections
Phase 3: Pilot Implementation (1-3 Months)
- Deploy initial solution in limited scope (single line, area, or facility)
- Document baseline metrics pre-implementation for accurate comparison
- Conduct iterative refinement of workflows and integration
- Develop training materials and begin workforce transition planning
Phase 4: Refined Deployment (3-6 Months)
- Expand implementation based on pilot learnings
- Scale training and change management efforts
- Implement continuous improvement processes
- Begin planning next-phase automation targets
This phased approach minimizes risk while allowing for learning and adaptation throughout the implementation process. Most importantly, it creates early wins that build organizational momentum.
Food & Beverage Sector Considerations: Automation in food processing requires specific attention to sanitation protocols and washdown-compatible equipment. IP69K-rated robots designed for direct food contact are now widely available, and vision systems can perform foreign object detection with greater consistency than human inspectors. The ROI equation also benefits from reduced contamination risk and extended shelf life through consistent handling.
Calculating the True ROI of Automation
Traditional ROI calculations often undervalue automation by focusing solely on direct labor replacement. A comprehensive ROI framework should include:
Direct Financial Impacts
- Labor cost reduction (calculated as hourly wage × hours offset)
- Overtime reduction (typically 15-30% with effective automation)
- Training and onboarding cost reduction (averaging $4,700 per warehouse worker)
- Workers' compensation and injury cost reduction (can reduce claims by 20-40%)
Operational Benefits
- Throughput increase (typically 30-200% depending on application)
- Accuracy improvement (error reduction often 20-80%)
- Consistency gains (process variation reduction 30-50%)
- Space utilization improvement (often 15-25% through optimized workflows)
Strategic Value
- Scalability during demand spikes (quantified as revenue protected)
- Business continuity enhancement
- Quality improvement (reduction in returns and rework)
- Customer satisfaction impact (measured through retention metrics)
Sample Calculation Framework:
3-Year ROI = (3-Year Total Benefits - Total Cost) / Total Cost
Where:
- Total Benefits = Direct Labor Savings + Indirect Labor Savings + Operational Benefits + Strategic Value
- Total Cost = Initial Investment + Implementation Costs + Maintenance + Training
For a typical warehouse AMR implementation supporting 15 workers, the 3-year ROI often ranges from 150-300%, with payback periods of 12-18 months at current labor rates.
Electronics Manufacturing Considerations: In electronics assembly, the precision of robotic systems can reduce defect rates by up to 65% compared to manual processes, particularly for miniaturized components. The ROI calculation should heavily weight quality improvements and rework reduction, which often exceed direct labor savings. Cleanroom-compatible robots also reduce contamination-related failures.
Transforming Your Workforce Alongside Technology
The human dimension remains critical to successful automation implementation. Effective transformation strategies share several key components:
Transparent Communication From Day One
- Share automation goals and reasoning before implementation begins
- Provide regular updates on project progress and learnings
- Directly address job impact questions with specific transition plans
Skills Transition Pathways
- Identify emerging roles (i.e., robot operators, fleet managers, maintenance technicians)
- Create clear skill development roadmaps for current employees
- Provide structured training opportunities with certification paths
Engagement Through Participation
- Include frontline workers in process design and refinement
- Create technology champion roles on each shift or in each department
- Implement suggestion systems for continuous improvement
Success Metrics Beyond Labor Reduction
- Develop and publicize metrics for quality improvement
- Track and celebrate productivity increases
- Recognize and reward innovation and process improvement
One manufacturer found that forming implementation teams with 50% frontline workers not only improved adoption but led to 30% more process improvement suggestions during the first six months after deployment.
Technology Selection Framework
With hundreds of automation solutions available, selecting the appropriate technology is critical. This framework provides a structured approach to evaluation:
Process Characteristics Assessment
- Volume and Variability: High-volume, low-variability processes typically justify higher automation investment
- Precision Requirements: Processes requiring consistent precision are strong automation candidates
- Physical Demands: Tasks causing ergonomic strain offer dual benefits through automation
- Decision Complexity: Processes requiring simple decision trees are easier to automate than complex judgment
Technology Capability Matching
- Pick and Place Operations: 6-axis robots or cobots with appropriate end effectors
- Transport and Movement: AMRs, AGVs, or conveyor systems
- Packaging and Palletizing: Purpose-built palletizing robots or cobots
- Quality Inspection: Vision systems and AI-enabled detection
- Machine Tending: Cobots with process-specific programming
Integration Requirements
- WMS/ERP Compatibility: Ensure bidirectional communication capabilities
- Data Collection: Evaluate analytics and reporting capabilities
- Physical Infrastructure: Assess space, power, and network requirements
- Scalability: Determine capacity for additional units and expanded scope
Vendor Evaluation Criteria
- Implementation Support: Assess training, programming, and deployment assistance
- Service Network: Evaluate response time and parts availability
- Track Record: Review implementations in similar applications and industries
- Financial Stability: Ensure long-term viability and support
This structured approach helps match specific operational needs with appropriate technologies while considering the broader implementation context.
Chemical Processing Considerations: Automation in chemical processing environments requires specialized equipment rated for hazardous environments (often with ATEX or similar certifications). The ROI calculation should heavily weight risk reduction and regulatory compliance benefits. Remote operation capabilities of modern robotics can reduce personnel exposure to hazardous conditions by up to 90% in some applications.
Integration with Existing Systems: The Keys to Success
Most manufacturing and supply chain operations have significant investments in existing technology systems. Successful automation implementations carefully address these integration points:
Enterprise System Integration
- WMS/ERP Connections: Establish bidirectional data flows for inventory and order information
- MES Integration: Ensure production planning systems incorporate automated components
- Quality System Alignment: Connect automation data with quality management systems
Data Architecture Considerations
- Standard Communication Protocols: Prioritize solutions using established protocols (OPC UA, MQTT)
- Edge vs. Cloud Processing: Determine appropriate data processing location based on latency requirements
- Historical Data Management: Establish retention and analysis frameworks for automation-generated data
Physical Infrastructure Requirements
- Network Infrastructure: Assess Wi-Fi coverage, bandwidth, and security for connected systems
- Power Systems: Evaluate electrical capacity and backup power requirements
- Space Utilization: Consider docking stations, maintenance areas, and human-machine interaction zones
Most failed automation implementations trace back to integration challenges rather than the core technology itself. A thorough assessment of these requirements before selection significantly improves success rates.
Beyond Labor Replacement: The Business Case Strengthens
While directly addressing workforce gaps provides the initial justification for automation, the financial benefits extend much further, strengthening the case for accelerated adoption.
The Economics Continue to Improve
The financial model for robotics implementation has evolved dramatically, reducing barriers to entry. Robotics-as-a-Service (RaaS) models grew 40% faster than traditional purchase arrangements by 2019, allowing operations to implement solutions without massive capital outlays.
"We shifted from thinking about this as a capital project to viewing it as an operating expense that scales with our business," explained a logistics director who recently implemented a RaaS solution. "That completely changed our financial analysis and accelerated approval."
The economic impact of successful implementations can be substantial. Amazon's robotics systems, for example, have reduced operating costs by 20 cents per package – a seemingly modest amount that translates to billions in savings across their volume.
Productivity Gains Compound Over Time
The productivity improvements from automation extend beyond direct labor offsets. McKinsey analysis indicates that automation could raise manufacturing productivity by 0.8-1.4% annually through 2030 – a cumulative effect that significantly enhances competitive positioning over time.
These improvements represent a fundamental shift in operational capacity. Rather than simply maintaining output with fewer workers, advanced implementations enable higher output with stable workforces – effectively decoupling growth from labor availability.
"We initially looked at robotics as a way to fill empty positions," a manufacturing executive noted recently. "Now we see it as the key to growing our business without having to solve an impossible hiring equation."
Implementation Challenges and Mitigation Strategies
While the case for automation has strengthened considerably, implementation still presents significant challenges. Understanding and proactively addressing these challenges is essential for success.
Investment and Financial Challenges
The capital requirements for automation implementation remain substantial. A single autonomous mobile robot typically costs between $30,000-$50,000, though emerging RaaS models have lowered the initial barrier.
Mitigation Strategies:
- Utilize RaaS models to convert capital expenditure to operating expense
- Implement in phases with clearly defined success metrics for each stage
- Consider vendor financing options specifically designed for automation projects
- Explore manufacturing extension partnerships and grants for small/mid-sized manufacturers
Workforce Resistance and Adoption
The human dimension remains critical. Gartner research found that 40% of workers express distrust toward automation initiatives, potentially derailing even well-designed implementations.
Mitigation Strategies:
- Begin communication well before implementation, focusing on how automation supports (not replaces) workers
- Create specific transition plans for affected employees
- Identify and empower internal champions across different departments and shifts
- Implement suggestion programs that reward process improvements incorporating automation
Technical Limitations and Integration Challenges
Current technologies, while advancing rapidly, still have significant constraints. Only 33% of C-suite executives believe they can rely solely on automation, with most implementations requiring meaningful human oversight.
Mitigation Strategies:
- Begin with proven applications rather than cutting-edge use cases
- Develop clear contingency workflows for system interruptions
- Implement comprehensive testing in parallel with existing processes before cutover
- Engage vendors with industry-specific implementation experience
Heavy Industry Considerations: In heavy manufacturing environments, the safety benefits of automation are particularly significant. Robotic systems for tasks such as foundry operations, heavy lifting, and hazardous processes can reduce recordable injuries by 50-70%. These safety improvements should be quantified as part of the ROI calculation, including both direct costs (claims, lost time) and indirect benefits (improved morale, reduced turnover).
Future Trajectory and Strategic Planning
Looking ahead, the integration of automation and robotics in manufacturing and supply chain operations is accelerating, driven by both necessity and opportunity.
Scale and Growth Projections
Gartner projects that by 2028, smart robots will outnumber frontline workers in manufacturing and logistics operations – a transformation that will fundamentally reshape industrial work.
The IFR forecasts robot installations reaching 600,000 units annually by 2025, up from 381,000 in 2017, reflecting both replacement of aging systems and expansion into new applications and industries.
Capability Advancements to Watch
The technical capabilities continue advancing rapidly. Machine learning integration enables robots to handle increasingly complex tasks with minimal programming, while improved sensing technologies expand the environments where automation can effectively operate.
Perhaps most significantly, the integration of robotics with broader intelligent systems – including predictive analytics, digital twins, and autonomous planning – is creating comprehensive solutions to workforce challenges rather than isolated point solutions.

Making This Work: The Leadership Challenge
Manufacturing and supply chain leaders face a defining challenge: navigating the transition to more automated operations while maintaining production capabilities and organizational cohesion. Here's how to approach this complex transition:
Timing Considerations
Given the projected 2.1 million worker gap by 2030, deferring automation investments likely represents a higher risk than moving forward, even in uncertain economic conditions.
Consider a portfolio approach that balances immediate tactical implementations (addressing current pain points) with strategic investments in more comprehensive solutions. Start with proven applications where the ROI is clearest, then expand based on experience and demonstrated success.
Workforce Evolution Strategy
Rather than viewing automation as a workforce replacement strategy, focus on workforce evolution – developing transition paths that allow existing employees to move into higher-value roles as robotics handles more routine tasks.
This approach addresses both immediate labor constraints and long-term skill development needs. Your most valuable future employees may already be on your payroll – just in roles that will be transformed by automation.
Technology Flexibility
As the technology landscape evolves rapidly, maintaining implementation flexibility becomes increasingly important. Evaluate both technology partners and implementation approaches based on adaptability and scalability rather than simply current capabilities.
"The robotics solution we implement next year will likely look quite different from what we put in five years ago," notes a manufacturing technology leader. "Building that expectation into our planning has been essential."
Conclusion: From Challenge to Competitive Advantage
The role of automation and robotics in manufacturing and supply chain operations has fundamentally shifted. What began as tactical responses to acute labor shortages have evolved into strategic imperatives that will shape competitive positioning for years to come.
The data tells a compelling story: with a 2.1 million worker gap looming by 2030, technologies that can offset 20-30% of labor requirements while simultaneously improving productivity represent not merely a solution but a necessity. Leading organizations such as DHL, Amazon, and BMW have demonstrated that thoughtful implementation can directly address workforce constraints while positioning for future growth.
For manufacturing and supply chain leaders, the question isn't whether to invest in automation and robotics – it's how quickly and comprehensively these technologies can be integrated into operational models. Those who move decisively while addressing the human, technical, and financial dimensions of this transition will likely emerge with significant competitive advantages in an increasingly constrained labor environment.
The labor shortage presents a genuine challenge. However, strategic automation implementation can transform it into a catalyst for operational excellence and sustainable competitive advantage.
About Partsimony
Partsimony helps hardware teams scale faster with fewer resources via adaptive manufacturing supply chains that provide a decisive competitive edge.
To get more done faster and with fewer resources, reach out to solutions@partsimony.com.
-------
This analysis draws on data from multiple authoritative sources, including Deloitte, the International Federation of Robotics, McKinsey, Supply Chain Dive, and the Quarterly Survey of Plant Capacity Utilization. All statistics cited reflect the most recent available data as of March 2025.
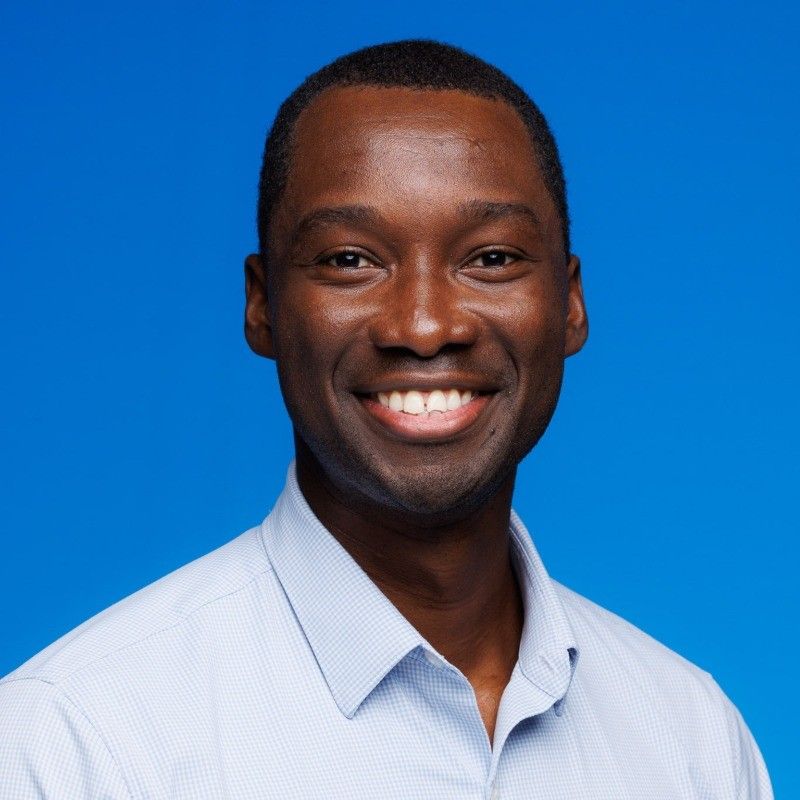
Rich Mokuolu
Supply Chain Strategist
Stay Updated
Get the latest insights on supply chain innovation and hardware development.